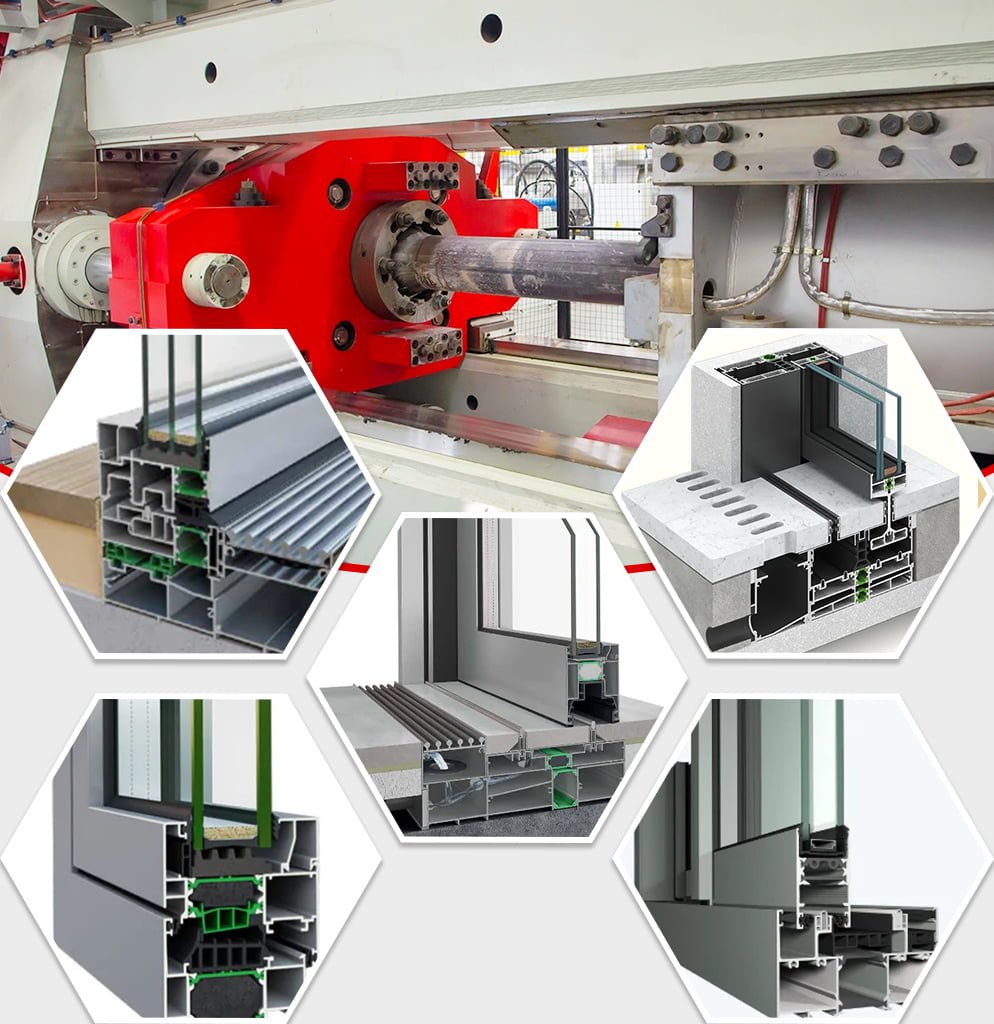
Metal extrusion is the manufacturing process of choice when producing high volumes of material with a constant cross-section. With the extrusion process, metal material is forced through the shaped opening of a die using high pressure, resulting in an extruded profile. These profiles range from simple shapes like round or rectangular tubes, U- or H-channels, or more complex profiles with multiple internal hollows and external features, such as 80/20 and T-slot framing bar. Extrusion is also standard for wall and window trim as a cosmetic and structural framing component. The raw material typically comes in billet form, which is heated and placed into part of the extrusion press called the container. A die stack sits on the other end of the container, forming the opening, which shapes the material to the desired shape using direct or indirect extrusion methods. The extrusion is then quenched, straightened, sawed to the specified length, and inspected for dimensional consistency and accuracy. Extruded products can easily be post-processed to add features outside the channeled profile.